Page 1 of 2
my experience forming 20vt brass
Posted: Wed Jan 22, 2014 5:03 am
by fishnbob
Just wanted to share my first experience forming 20 vt brass from once fired lc brass.
First I took RIO,s advice and bought redding 3 die competition set. It included a body die, type s neck bushing die, and a competition seater die.
I experimented with a few different things and this is my final process that I ended up with and have finished 300 pieces so far.
First I take all the internal parts out of the bushing die, put a little imperial wax on the case and make 1 pass through the die.
The necks come out extremely long, so I cut them down on a chop saw and then chamfer the outside of the necks so they are smooth for the next step.
Second I run them through the body die and then do a final trim length.
The body die leaves the inside of the neck a perfect size that I dont have to use the expander and they are ready to neck turn.
I then turn the necks to the desired size.
Then I chamfer inside and outside of the neck, uniform the primer pocket and debur the flash hole.
I then anneal and my third and final step is to run them through the bushing die with the bushing and the expander ball installed in the neck die. Then load and shoot.
This is my first group shot with my new cooper with my newly formed brass.
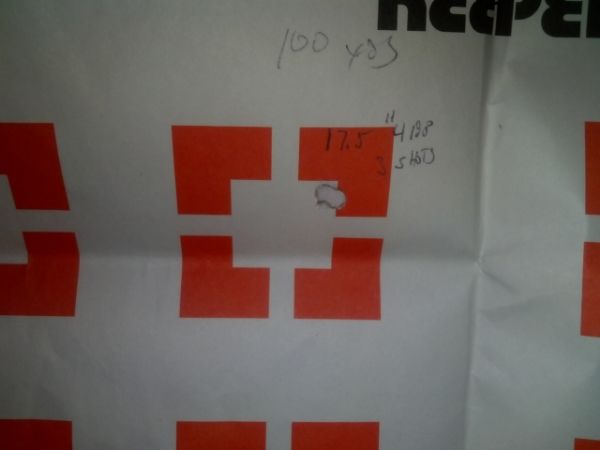
It was a little intimidating at first but today I am going to make up another 500 pieces.
It looks like the process and the rifle show some great potential. I know it is only a 3 shot group but I didnt have much brass made up yet and didnt want to make much until I was sure what type of accuracy I was going to get.
I think it just might work.
Re: my experience forming 20vt brass
Posted: Wed Jan 22, 2014 4:58 pm
by acloco
WOW! Lets see some pictures of the brass after each step.
GREAT group!!!!
Re: my experience forming 20vt brass
Posted: Wed Jan 22, 2014 10:43 pm
by Sidewinderwa
Nice group for sure. Is lc brass, Lake City 5.56 brass?
Re: my experience forming 20vt brass
Posted: Thu Jan 23, 2014 7:59 am
by fishnbob
Yes it is 5.56 lake city and I will get some pics of the process here soon.
Re: my experience forming 20vt brass
Posted: Thu Jan 23, 2014 8:08 am
by Rick in Oregon
Very nice indeed there, Bob. Don'tcha just love it when a plan comes together?

Re: my experience forming 20vt brass
Posted: Fri Jan 24, 2014 1:59 am
by Bodei
Pretty much my process too except I use the Redding .223-.221FB forming die as the first step, resulting in less case damage. What are you turning the necks to? .012"? There is a lot of satisfaction in making this brass, but it sure is a ton of labor!
Re: my experience forming 20vt brass
Posted: Fri Jan 24, 2014 6:49 am
by fishnbob
Bodei wrote:Pretty much my process too except I use the Redding .223-.221FB forming die as the first step, resulting in less case damage. What are you turning the necks to? .012"? There is a lot of satisfaction in making this brass, but it sure is a ton of labor!
I dont have the tools to measure the neck thicness but I turn them so the outside diameter is .228 loaded and I measure with a micrometer.
Re: my experience forming 20vt brass
Posted: Sun Jan 26, 2014 7:19 pm
by Bodei
I just pretty much use my calipers to measure neck thickness since I turn the necks with a K&M tool.
Re: my experience forming 20vt brass
Posted: Mon Jan 27, 2014 9:06 pm
by fishnbob
Bodei wrote:I just pretty much use my calipers to measure neck thickness since I turn the necks with a K&M tool.
Bodei
Thats what I use is the K&M. I measured with my caipers tonight and it looks like it is about .0125. I have the pieces to show the steps I just need to get a photo and get them loaded into my photobucket. I should have them up soon.
Re: my experience forming 20vt brass
Posted: Mon Jan 27, 2014 9:40 pm
by Jim White
fishnbob wrote:
I dont have the tools to measure the neck thicness but I turn them so the outside diameter is .228 loaded and I measure with a micrometer.
What you need is a "tube-micrometer". I've found they are far more accurate for neck thickness than regular calipers.
HTH
Re: my experience forming 20vt brass
Posted: Mon Feb 17, 2014 8:04 pm
by fishnbob
Here are the steps. I didnt include pictures of every one because they probably would not be noticeable. First one is through the bushing die with the bushing removed. The second one was trimmed and through the body die and the third one is necked tuned, final trim, chamfer , annealed and loaded. Sorry the pics aren't that great.
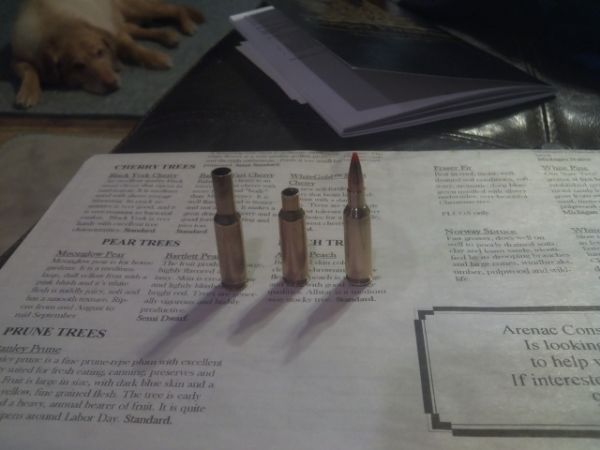
Re: my experience forming 20vt brass
Posted: Tue Feb 18, 2014 11:54 pm
by Bodei
Looks good!
Re: my experience forming 20vt brass
Posted: Wed Feb 19, 2014 8:53 am
by inKYfromSD
Nice job on the brass, and the group! I've tried removing the "guts" from the bushing die but the brass just gets crushed. I have better luck using the body die and just a touch of Imperial wax on the base-end of the brass. I wonder if the brass I'm using is already too hardened? Does full-length sizing it in a .223 beforehand matter? I have 500 pieces of virgin Nosler .223 brass. Maybe I'll try 20 of those and see what happens. I think I may have had too much wax on the case and ruined it with the hydraulic pressure. I don't need to rely on forming it from .223/5.56 since I have a bunch of .221 FB brass but forming it is fun and keeps me out of trouble.
How are you trimming the excess neck? I used a make-shift jig and a 32 TPI hacksaw but it's a PITA.
Re: my experience forming 20vt brass
Posted: Wed Feb 19, 2014 9:00 am
by Rick in Oregon
inKYfromSD wrote:How are you trimming the excess neck? I used a make-shift jig and a 32 TPI hacksaw but it's a PITA.
Brian - Some of the guys over on Saubier are using the little Harbor Freight chopsaw to cut the long neck on formed 5.56 brass to 20VT. You need a holding device, but it seems to work very well over the PITA hacksaw operation. HTH
Re: my experience forming 20vt brass
Posted: Wed Feb 19, 2014 4:37 pm
by TrapperDan
I just completed turning 600 pieces of 223 into 20 VT but used a different approach for cutting the long necks to length. I clamped a 2x4 to the bench. Drilled a 7/16" x 1-3/16" deep hole in it close to the edge. I then took a piece of 1”x 2” x 3/16” scrap steel and drilled a ¼ “ hole in the center of it. I would put a necked down 223 case into the hole in the 2x4 , place the piece of steel over the neck and use my 4” grinder with a thin cut off wheel on it to cut the neck off flush .I could do 100 cases in 10-12 minutes. I used layers of black plastic electrical tape on each end under the steel to adjust to the proper height ( length.) I would leave the length about.010 long and clean it up with my case trimmer. Only problem is that I don’t have a cooper to shoot them in.